

Make sure to take notes on the number of windings, the orientation and the order how the coils. Depending on how the coils were secured it helps to apply some heat to soften any glue. Remove the solder joint by cutting the wires using a sharp cutting plier and start by unwinding the first coil. Remove any heat shrink and gently untwist the connection. For the Racerstar BR1103B the best part for the start of unwinding is the star point junction.

I use a burned old stator for that purpose. I could not find a scientific reference on that (if you do please let me know!) but it might be a good idea to do so. Some people recommend not to leave the rotor without a stator for longer periods of time, the magnetic field lines will not be closed and the magnetization can degrade. Start the disassembly by removing the C-Clip and lift of the rotor. Most likely you will start with a motor that is already wound and you will apply the same winding scheme. It is possible to convert a motor from Delta and Wye and vice versa by changing the solder connections and scheme of the coils. There is no physical neutral point available.ĭelta terminated motors spin 1.7 times faster than a Wye termination whereas a Wye terminated motor has 1.7 times the torque of a Delta terminated motor. The three pairs of two coils are connected together and routed to the outside. The other termination scheme is called Delta termination. The motors used in RC applications typically does not have this connection lead to the outside and a heatshrink makes sure it does not create a short circuit. This motor uses the so called Wye or Star termination scheme: The starting ends of three coils are connected together and form a neutral point. There are two possible ways to connect the six endings of those three winding wires: The windings on such a motor are made out of three long wires, wound in a special configuration around multiple shoes. In this case there are twelve magnets mounted in the rotor which results in a popular 9N12P configuration.Īs the name suggest, a three phase motor has three motor phases and you usually connect it to the speed controller with three wires. There are some popular combinations that are used the most. The number of magnets in the rotor can vary. In the case of the BR1103B you can count nine stator shoes. For three phase brushless motors, the number of stator poles is always a multiple of three.
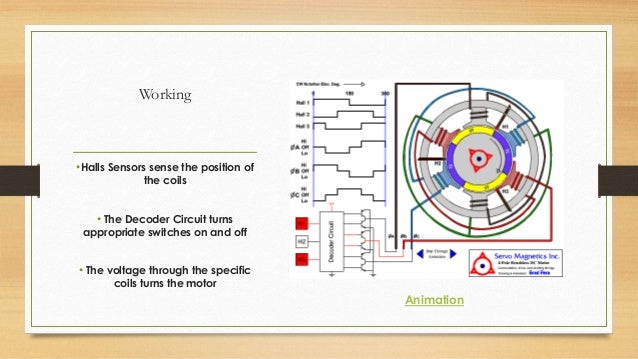
The stator is made of thin metal sheets and several windings of copper wire form electromagnets that can create magnetic fields that can be controlled by your ESC. The following picture shows the main components I am going to talk about in this post:ĭuring motor operation the axis of the rotor, shown on the left, is held in place by a c-clip, lock screw or a similar fastener. The basicsīefore starting with the tutorial I want to give a short overview on the parts of an outrunner brushless motor. Even though this tutorial is based on the BR1103B, the basic steps for motor rewinding are the same for all outrunner brushless motors. The stock motor comes in 8000 KV and 10000 KV, my goal is to add a 4500 KV and 6500 KV variant to this lineup by rewinding a stock motor. I am planning to do some thrust and efficiency tests in the near feature and I need some special KV versions of the good old Racerstar BR1103B motor that you can not yet (?) buy.
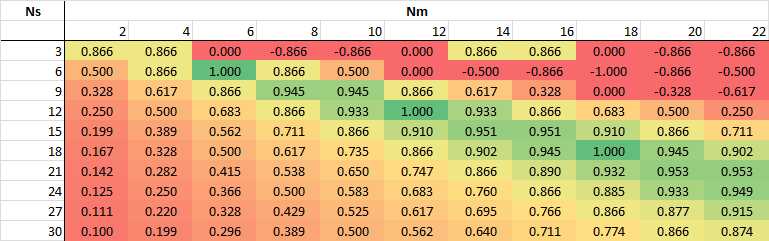
Most of the time the manufacturer should list the KV rating and there is no reason for them to give you a fake rating.
#Brushless motor winding calculator how to#
If you have read my previous tutorial on how to measure the KV rating of a brushless motor you might be still wondering why you should ever need to do KV measurements on your own.
